Analysis of an existing hydrocarbon gas pipeline for conversion to dense phase CO2 service
David Levy A *A
![]() David Levy has 15 years’ experience in the oil and gas industry and is currently the Senior Integrity Engineer with Esso Australia. He previously held the role of Senior Subsea, Pipeline & Riser Engineer with Esso Australia, and is a pipeline subject matter expert for the affiliates offshore and onshore pipeline network and Low Carbon Solutions business. He holds bachelor’s degrees in mechanical engineering/aerospace technology from Monash University and an MBA from Australian Institute of Business. He is Chartered with Engineers Australia and holds AMPP/NACE CP2 Certification. |
Abstract
Esso Australia is investigating the feasibility of a carbon capture and storage (CCS) project in East Gippsland, Victoria. Known as the South-East Australia Carbon Capture and Storage (SEA CCS) Hub, the project aims to re-purpose existing infrastructure and offshore depleted hydrocarbon reservoirs to store carbon dioxide (CO2). The project aims to reduce greenhouse gas emissions from Esso’s Longford Gas Conditioning Plant, and to unlock future CCS opportunities for Australia. One option identified as part of the SEA CCS feasibility was to convert part of the existing onshore section of the Barracouta 450 mm gas pipeline to Longford Gas Plant (BTA450-LFD), Licence PL/1 under the Victorian Pipeline Act, to dense phase CO2 service. This paper documents the initial findings of the potential for the onshore section of the BTA450 for conversion, with particular emphasis on brittle and ductile fracture control considerations. In summary, when attempting to convert existing hydrocarbon gas pipelines for CO2 service, operators need to undertake an appropriate assessment of fracture control considerations. The insights of this paper may serve as a useful guide document for assessing other existing onshore pipelines for CO2 service conversion. Due to the thermal modulation effect of the surrounding water for subsea pipelines, this guidance does not apply to subsea pipeline sections.
Keywords: AS 2885, brittle fracture, carbon capture, CCUS, CO2, DNV-RP-F104, ductile fracture, emissions reduction, fracture control, Gippsland, Gippsland Basin, low carbon solutions, pipelines.
Introduction
ExxonMobil established its Low Carbon Solutions (LCS) business to commercialise the company’s extensive lower-emission portfolio with the objective to create long-term shareholder value and support global emissions-reduction efforts. Currently, LCS is focussed on commercialising lower-emission business opportunities in carbon capture and storage (CCUS), hydrogen (H2) and lower emission fuels, by leveraging the skills, knowledge, and scale of ExxonMobil.
As part of these opportunities, Esso Australia on behalf of the Gippsland Basin Joint Venture (GBJV) is undertaking early feasibility/Front End Engineering Design (FEED) to determine the potential for CCUS to reduce greenhouse gas emissions from multiple industries in the Gippsland Basin. Announced as the South-East Australia Carbon Capture and Storage (SEA CCS) Hub, the project aims to initially take dense phase CO2 from the Longford Gas Conditioning Plant via pipeline to the Bream A platform in offshore Bass Strait, where the CO2 will be permanently injected in the Bream reservoir. Ultimately the project aims to reduce large scale emissions in line with ExxonMobil’s and Australia’s carbon emission reduction goals.
The Barracouta 450 mm Gas pipeline to Longford was constructed in 1968 and transports produced gas from Barracouta A platform (BTA) to the Longford Gas Plant for processing and sale to Eastern Australia natural gas customers. In 2021, an additional flowline connection was made via subsea hot tap near BTA to flow the newly developed Barracouta West (BTW) field.
The pipeline is a 450 mm nominal diameter API 5L X52 carbon steel pipeline. The onshore section consists of double submerged arc welded (DSAW) pipe that’s predominantly 10.4 mm thick with short sections of 12.7 mm thick pipe at some road crossings. It’s coated with Coal Tar Enamel (CTE) coating for external corrosion protection which is further complemented via impressed current cathodic protection. It’s a licenced pipeline (PL/1) under the Victorian Pipelines Act.
As part of the SEA CCS feasibility study, an evaluation was made on a section of the BTA450 pipeline between Longford and Valve Site 3 for CO2 service.
The immediate advantages of this would be to eliminate the need for new pipeline construction and installation, remove associated requirements for a new pipeline right of way/easement, avoid associated environmental disturbances and disruption to landholders, and reduce start-up times for carbon sequestration.
Method
To convert the existing BTA450 pipeline section to CO2 service, a requalification process was required. This was required for two reasons:
to ensure that the design basis of the pipeline is re-evaluated, and all existing risks are reassessed to ensure the safe operation of the pipeline in CO2 service; and
to comply with regulatory obligations under the Victorian Pipelines Act, Pipeline Regulations, and AS 2885.
A requalification process for CO2 service includes several factors (DNV 2021). The process includes evaluation of integrity information, flow assurance and hydraulic analysis and associated safety implications of changing the process fluid to CO2. Australian Standards (AS/NZS 2018a, 2018b, 2022) are also descriptive of the required changes, in terms of consequence modelling for CO2 exposure, management of change and fracture control requirements.
The assessment identified a total of 57 high-level items that need to be considered as part of the BTA450 conversion (Table 1). These were assessed using a traffic light ranking system to determine the acceptability of the pipeline for CO2 service, identify any modifications that are required, and any potential STOP items that would render the pipeline unsuitable for CO2 service.
Consideration | # Findings | Comments | |
---|---|---|---|
Safety | 6 | The safety implications are relatively well understood, with both DNV and ExxonMobil consequence modelling for a dense phase CO2 loss of containment being analogous to the current 4.7 kW/m2 consequence distances recommended in AS/NZS (2022) risk management. This model is based on the relatively flat topography between valve site 3 and Longford. A Safety Management study is still required for the pipeline for CO2 service. | |
Environmental | 8 | No significant difference to existing oil/gas hydrocarbon pipelines. | |
Integrity | 17 | The key integrity issues identified for further assessment include (a) the introduction of internal corrosion mechanisms due to accidental insufficient dehydration of the process stream, (b) ILI tool compatibility, (c) non-metallic material compatibility (i.e. elastomeric seals in valves/instruments), and (d) fracture control requirements. | |
Capacity | 5 | Transport capacity pipeline hydraulics detailed sensitivities due to variations in product temperature, particularly during transient conditions such as start-up, cool down and restarts. | |
Operability | 10 | Key issues identified include the introduction of surge over-pressure issues (due to incompressibility of dense phase CO2 versus hydrocarbon gas), issues around rate of venting and composition monitoring to ensure the onstream specifications are maintained. | |
Availability | 2 | No significant difference to existing oil/gas hydrocarbon pipelines. | |
Maintainability | 2 | No significant difference to existing oil/gas hydrocarbon pipelines. | |
Regulatory | 7 | As a relatively new industry, many of the items identified relate to regulatory approvals and follow-up conditions required to alter the existing Pipeline Licences for CO2 service. Continuous regulator engagement and consultation should be maintained. |
Modelling was performed by Esso Australia to demonstrate the difference in relative cooling effects of hydrocarbon gas versus dense phase CO2. The models attempted to simulate the sudden isentropic decompression of both CO2 and hydrocarbon gas (90% methane, 5% ethane, 5% propane) process streams from 10,000 kPa to ambient condition through a choked 10 mm hole to determine the degree of temperature drop and thermal energy transfer from the fluid to the surrounding environment (i.e. soil and pipe). The 10 mm choked hole was to simulate a corrosion hole failure scenario.
Discussion/results
The challenges in maintaining ongoing structural integrity of CO2 pipelines are outlined below.
Internal corrosivity
Experience and experiments suggest the rate of internal corrosion is very low in pure or dry CO2 service (due to lack of free water for carbonic acid formation). However, even low to medium CO2 partial pressures can result in significant and severe corrosion rates in flow streams where free water and some contaminants (particularly O2, SOx or NOx) are present.
Low-temperatures (brittle fracture) concerns
CO2’s significant Joule-Thompson expansion-induced cooling effects can readily induce temperatures as low as −20°C, or theoretically as low as −90°C in the event of a loss of containment and sudden decompression down to ambient pressure (e.g. rupture or emergency blowdown).
As demonstrated from the modelling above (Fig. 1), there can be significant differences in both minimum temperature and heat transfer capacity between a gaseous hydrocarbon leak and a dense phase CO2 leak. Should this occur on a buried section of an onshore pipeline, there can be significant brittle fracture initiation concerns.
Theoretical heat transfer and minimum temperatures on a small leak from a gaseous hydrocarbon pipeline (left) versus a dense phase CO2 pipeline (right). The results indicate a significant variance in both temperature (−47°C versus −90°C respectively) and overall heat transfer (9.1 × 105 versus 99.9 × 105 kJ/h respectively).
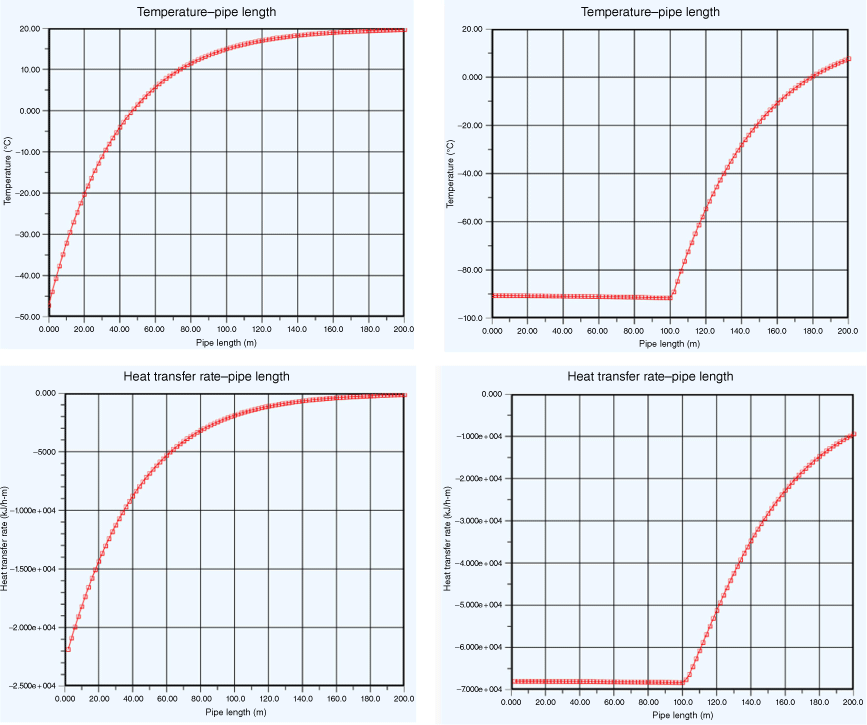
Brittle-to-ductile fracture control concerns
The advent of significant low-temperature excursions that could be reached in a dense phase CO2 leak can be significant fracture control considerations. Despite this pipeline, like many other pipelines, demonstrating ‘no rupture’ design in accordance with AS/NZS (2022) requirements, the low temperature impacts of a leak of dense phase CO2 could introduce the possibility of a brittle-to-ductile failure mode.
A flowchart of this potential failure mechanism is detailed below in Fig. 2.
Flowchart detailing the possible Brittle-to-Ductile fracture failure mode mechanism within a CO2 pipeline.

Existing gas hydrocarbon pipelines are generally designed with a −10°C/0°C minimum design temperature, which is verified against Drop Weight Tear Tests (DWTTs). Since CO2 leaks can generate much colder temperatures, particularly in buried sections, this has the potential to impact the adequacy of this brittle fracture initiation control.
A small pinhole corrosion leak on a buried section of a CO2 pipeline could induce very low process fluid temperatures. Continued exposure to these very low temperatures for extended periods could cool the line pipe to below its minimum design material temperature (since CO2 has the potential to introduce temperatures well below typical gaseous hydrocarbon minimum temperatures). This could result in a brittle fracture initiation event.
Brittle fractures are characterised by a rapid propagation of a crack-like flaw within the cooled material. If the flaw length approaches the critical defect length of the pipeline, even if the line pipe is above the Minimum Design Material Temperature (MDMT), this could result in a change in crack propagation from a brittle fracture-driven to a ductile-tearing (fast running) fracture.
Since CO2 pipelines generally require higher arrest toughness than gaseous hydrocarbon services, it is likely the pipeline may have insufficient toughness to arrest this fracture propagation. This is despite a pipeline typically having sufficient toughness for ductile fracture arrest in gaseous hydrocarbon gas service.
The result of this failure mode would have Safety, Environmental and Supply impacts.
Summary and conclusions
The results of this study identified the risk of a ‘brittle-to-ductile’ fracture failure mechanism in existing hydrocarbon gas pipelines when converted to dense phase CO2 service. Pipeline engineers and designers involved in conversions of existing hydrocarbon gas pipelines to dense phase CO2 service should take care of existing brittle and ductile fracture controls and ensure that these controls and their underlying assumptions are confirmed as part of the conversion assessment works.
The selection and adequacy of minimum design material temperatures for line pipe materials for CO2 service and associated brittle fracture failure modes should be an area of further research, as well as any impacts various pipeline configurations (pressure, temperature, pipe wall thickness, pipe toughness properties, pipe glass-transition temperature limits, fluid composition, un-isolated versus isolated flow, exposure times, etc.) have on brittle fracture initiation control.
Additional research to expand the limits of the DNV (2021) methodologies for fracture control would aid in the conversion assessments of existing pipelines. The current DNV (2021) ductile fracture toughness calculations are limited to specific grades, wall thicknesses, diameters, and other dimensions. Due to the prospects of further conversion assessments across the hydrocarbon industry, a wider range of variables should be qualified.
Data availability
Data sharing is not applicable as no new data were generated or analysed during this study.
Acknowledgements
I’d like to acknowledge all my colleagues, supervisors and managers within ExxonMobil who supported me during the preparation of this paper and supported my previous and current research on this topic.
![]() David Levy has 15 years’ experience in the oil and gas industry and is currently the Senior Integrity Engineer with Esso Australia. He previously held the role of Senior Subsea, Pipeline & Riser Engineer with Esso Australia, and is a pipeline subject matter expert for the affiliates offshore and onshore pipeline network and Low Carbon Solutions business. He holds bachelor’s degrees in mechanical engineering/aerospace technology from Monash University and an MBA from Australian Institute of Business. He is Chartered with Engineers Australia and holds AMPP/NACE CP2 Certification. |