Properties and antifouling performance of fabricated polymers containing copper thiocyanate
Krishnamurthy Prasad A , Richard F. Piola B , Jitraporn Vongsvivut C , Hareem Khan D , Paul J. Molino D , Dominic J. Hare
A
B
C
D
Abstract
Fouling of subsurface structures by micro and macro-organisms is a centuries-old problem that can be better managed by the use of multi-functional materials and modern fabrication techniques. Copper(I) thiocyanate, or CuTC, is a common coordination polymer that reduces the adherence and growth of marine organisms on underwater surfaces used as a paint additive. Test samples of polymers that contained up to 20% (w/w) CuTC were fabricated using two methods: a two-part epoxy system, cast into moulds and cured at room temperature; and stereolithography, a 3-D printing technique that uses UV light to set designs additively manufactured from a single part urethane resin. Fabricated materials were extensively characterised by advanced X-ray diffraction (XRD), scanning electron microscopy (SEM) and polarised synchrotron Fourier transform infrared (S-FTIR) microspectroscopy, which together revealed distinct molecular networking structures within the added chemical biocide that depended on the manufacturing method used. Performance was tested over a 3-month deployment, which showed marked differences in the effectiveness of the fabricated material types in resisting fouling by aquatic organisms in a static estuarine environment. These differences are attributable to distinct physical and chemical properties of the test materials imparted upon them by the fabrication method, all of which are areas for further investigation in the development of manufactured fouling-resistant polymers for use in marine environments.
Keywords: antifouling, antimicrobial, composite materials, copper thiocyanate, fouling-resistant materials, marine fouling, metal–organic frameworks, stereolithography, synchrotron Fourier transform infrared microspectroscopy.
Introduction
The adherence and growth of marine organisms on artificial structures is an inevitable consequence of human activity in aquatic environments. Starting with the formation of thin molecular films, interactions between the substrate, bacteria and other eukaryotes eventually lead to communities of increasingly more complex marine organisms becoming established on once clean surfaces.1 Negative effects arising from fouled subsurface structures include loss of function, such as preventing machinery from performing tasks or decreasing the efficiency of hydrodynamic surfaces, as well as the substantial environmental consequences of improper management.2
Fouling of a clean submerged surface generally follows a four-step process: macromolecular conditioning films composed of inorganics, polysaccharides and proteins form at the surface interface; followed by a microbial biofilm composed of passing aquatic microorganisms; and then algal spores, marine fungi and protozoa; before the eventual colonisation by spawn of larger invertebrates like arthropods and photosynthesising macroorganisms.3 The biofilms that eventually foul artificial structures are also important ecological drivers of aquatic species diversity and interactions and their formation follows a complex and dynamic set of geochemical and environmental cues.4
Functionalising materials to incorporate an antimicrobial agent is a direct approach to slowing biofouling and reducing the impact it has on subsurface structures. Different approaches have used surface coatings containing chemical biocides (which has traditionally included paints and now encompasses a wide range of coatings with antimicrobial properties)5; conditioning of the surface to mechanically disrupt the formation of film-substrate bonds6; synthesising biomimetic polymers with interfaces designed to replicate natural surfaces that are resistant to fouling7; applications of graphene-based materials, including functionalised nanomaterials and photocatalysers8; and responsive materials able to kill and release adherent bacteria from functionalised surfaces,9 to name just a few.
Innovative as many of these approaches are, eventual use in any fouling management strategy requires technology and fabrication methods that can be developed and tested at scale, while also incorporating standard materials and practice used in the maritime industry. Chemical additives like biocides remain an attractive option, as their use can be readily integrated into large-scale fabrication methods, such as additive manufacturing of composite materials. The decades following the withdrawal of overtly toxic materials like tributyltins (TBTs) from antifouling paints have also seen substantial research into so-called ‘green’ biocides that do not pose the same persistent pollutant threats as the heavy metal-containing compounds they are replacing.10
Copper(I) thiocyanate (abbreviated as CuTC; a coordination polymer with the empirical formula CuSCN) is one such organometallic compound that emerged as a replacement for TBTs, with CuTC-containing paints demonstrating antifouling activity with comparatively less harmful effects on marine environments.11 Copper compounds are often employed for their antimicrobial properties12 and when used in antifouling paints CuTC does perform better than copper(II) oxide (CuO) at preventing barnacle growth.13 Commercial CuTC-based paints release near-tenfold less copper than CuO into artificial seawater, though both compounds appear to release the same reactive Cu2+ ion into the environment once a surface reaches a steady state.14
Despite gaps in a detailed mechanistic understanding of CuTC as an antifouling agent, its performance has led to it becoming one of the six most commonly used biocide additives in fouling-resistant paints in Europe.10 Importantly, CuTC is also amenable to integration with flexible manufacturing methods, including use as a dispersible additive in 3-D printing. The prospect of manufacturing synthetic structures with inherent antimicrobial properties, combined with the established and characterised use of CuTC as an antifouling additive in the maritime industry, make it an ideal candidate to assess performance in extended environmental deployments. The emerging opportunities for 3-D printing and additive manufacturing in marine research15 and maritime industries16–18 are many and recent experiments have shown how 3-D-printed materials themselves have reduced fouling coverage after 12 weeks of seawater exposure.19
We applied CuTC as an additive to polymers produced using both a conventional two-part cast epoxy resin system and an additive manufacturing stereolithograhy (SLA) technique and then characterised its performance as the basis of fouling-resistant materials for use in maritime applications. We characterised 3-D-printed and cast polymer test samples doped with CuTC using polarised synchrotron Fourier transform infrared (S-FTIR) microspectroscopy, X-ray diffraction (XRD) and scanning electron microscopy (SEM), and observed divergent molecular properties of the CuTC depending on the fabrication method used. Detailed structural characterisation revealed distinct characteristics such as surface structure, morphology and chemistry all likely confer the differing performance of CuTC-based materials when tested in a true aquatic environment. The results obtained from this study support the further optimisation of scalable additive manufacturing methods for fabricating subsurface maritime structures using polymer-based materials.
Experimental
Fabrication of test samples
Cast resins were manufactured from very low viscosity epoxy KINETIX R118 with amine-based H120 hardener (ATL Composites, Australia). KINETIX R118 is formulated for vacuum infusion applications and produces moisture-resistant void-free laminates and the H120 hardener confers desirable mechanical properties from a room temperature cure. Test samples that were manufactured by SLA used 3-D Rapid TUFF (Monocure, Australia), a low viscosity, UV-curing (405 nm) urethane resin with comparable tensile strength and hardness to cast epoxy resin test samples. A single source of powdered CuTC (99% purity; Sigma–Aldrich, Australia) was used for both fabrication methods.
Circular discs ~5 cm in diameter were fabricated from 8 g of KINETIC R118, into which either 1 or 2 g of CuTC was added and rapidly stirred for 2 min to achieve dispersion. Hardener (2 g of H120) was then added and the mixture was stirred for a further 2 min. The viscous solutions were poured into circular aluminium moulds and cured at room temperature for 48 h. Control discs were also prepared from R118 and H120 only, producing the final three conditions of cast epoxy resins with 0, 10 and 20% (w/w) of added CuTC. (Fig. 1a).
Disc-shaped test-pattern designs were produced by SLA using a Photon M3 Max 3-D printer (Anycubic, China). Powdered CuTC was first added to clear 3-D Rapid TUFF resin at 10 or 20% (w/w) proportions, which was dispersed for 2 min on a VIBA 300 shaker (Collomix, Germany). After a 1-h-long print, the test samples were washed in isopropyl alcohol for 15 min and returned to the attached UV curing chamber for a 15-min initial curing cycle. Following another water rinse, a full 2-h curing cycle was applied. Samples of printed and UV-cured resin only were similarly prepared as the 0% (w/w) CuTC controls (Fig. 1b).
Analytical methods
The S-FTIR mapping measurements were performed on the Infrared Microspectroscopy (IRM) beamline at the ANSTO–Australian Synchrotron, using a Bruker Vertex 80v spectrometer coupled with a Hyperion 3000 FTIR microscope and a liquid nitrogen-cooled narrow-band mercury cadmium telluride (MCT) detector (Bruker Optik GmbH, Germany). All the S-FTIR spectra were recorded within a spectral range of 3900–750 cm−1 using 4-cm−1 spectral resolution. Blackman-Harris 3-Term apodisation, Mertz phase correction and zero-filling factor of two were set as default acquisition parameters in the Bruker OPUS 8.0 software suite.
The test samples were initially cut and imaged in macro ATR-FTIR mapping mode, using an in-house developed macro ATR-FTIR device equipped with a 250-µm-diameter facet germanium (Ge) ATR crystal (nGe = 4.0) and a 20× IR objective (NA = 0.60).20 Every synchrotron macro ATR-FTIR spectrum was collected with a beam defining aperture, providing a nominal measurement area of 3.1-µm diameter per pixel at 3-µm step interval, using 256 and 16 co-added scans for background and sample spectral acquisitions respectively.
To characterise the molecular orientation and crystallinity of the test samples, four-angle polarised-IR maps were acquired according to previously published methods using a pair of identical KRS-5 wire grid polarisers (Edmund Optics, USA).21 Briefly, the incoming beam polarisation was first fixed at 0° and the outgoing beam polarisation changed to 0, 45, 90 and 135°. For each sample, four spectral maps were collected at 0/0, 0/45, 0/90 and 0/135°, covering an area of 60 × 60 µm2.
Crystal structure and chemical composition of test samples were subsequently analysed using XRD technique. A benchtop D2 PHASER (Bruker) diffractometer with a Cu source (Kα = 1.54 Å) was used to collect XRD spectra over a 2θ range of 5°–75°, at a scanning rate of 0.02°s−1 and a dwell time of 1 s.
Surface characteristics and morphology were examined by SEM, using a Zeiss Supra 40 VP microscope.22 Specimens of the test material were snap-frozen under liquid nitrogen to expose cross sectional surfaces and then processed on an Emitech K975X gold sputter coater (Quorum Technologies, UK) prior to SEM analysis.
Marine fouling study
The performance of fabricated materials in resisting adherence and growth of marine organisms was tested in a 3-month environmental deployment, adapted from previously published methods.19 Experiments used a testing raft at a Defence Science and Technology Group facility in Williamstown on Port Phillip Bay (Victoria, Australia). Test samples were affixed to a polyvinyl chloride (PVC) board using 3-D-printed polylactic acid (PLA) clips and the board was then suspended between 0.5 and 1.5 m beneath surface depth. The PVC backing was coated with a commercial foul-release coating (Hempaguard X3, Hempel A/S) to minimise the influence of indirect biofouling. Samples were deployed in early-to-mid 2023, when Greater Melbourne received average-to-below average rainfall and warmer than average temperatures.23–25
Results
Characterisation of fabricated test samples
The dispersed white CuTC was observed to turn deep green-black that was visually reminiscent of copper oxidation during the curing process (shown in Fig. 1a). This was not observed in the 3-D-printed test samples, which remained the same off-white colour of the source CuTC powder.
The coordination environment of copper in fabricated test samples was examined using XRD (Fig. 2). Analysis of the diffraction patterns collected from neat CuTC identified high intensity peaks that mapped to both α (ICDD, formerly JCPDS, card number 29-0582)26 and β (ICDD card number 29-0581)27 crystal polymorphs of the CuSCN coordination polymer. These peaks were conserved in spectra from the 3-D-printed test samples, with a shift to lower 2θ suggesting expansion of the lattice structure. This alignment was absent in cast epoxy resins containing the same source CuTC, which produced distinct spectra with three prominent peaks emerging at 2θ angles between 11.3 and 19.4°. Diffraction patterns of both cast epoxy and 3-D-printed urethane resins without added CuTC reflected their amorphous, non-crystalline structures.
XRD patterns of neat CuTC and fabricated test samples. Spectra have been intensity-offset overlayed and overlayed with 10%-added CuTC compositions omitted to aid visual comparison. Peaks marked with arrows indicate the presence of copper-amine bonds in the 20% CuTC cast epoxy resin sample.
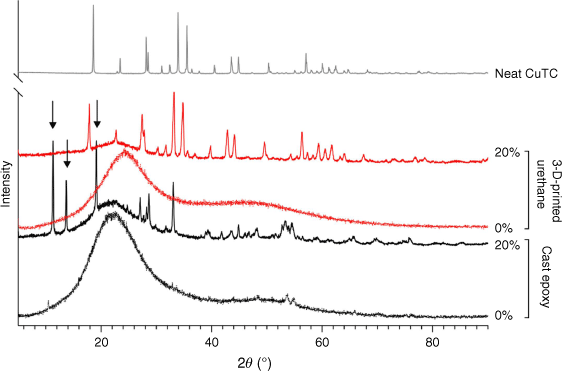
We used laboratory-based ATR-FTIR spectroscopy to examine the molecular composition of the fabricated samples doped with CuTC (Fig. 3). Spectra from neat CuTC powder contained distinctive peaks at ~2150 cm−1 and 740 cm−1 characteristic of ν(C–N) and ν(C–S) absorption, respectively, as well as δ(SCN) vibration at 412 cm−1.28 Inspection of the peak shapes corresponding to δ(SCN) vibration suggests a presence of α,β-dimorphism of the source CuTC material that was observed from XRD analysis; and, the distinctive ν(C–N) vibrations at 2152 and 2110 cm−1 in 3-D-printed samples were particularly reminiscent of the reported orthorhombic structure of the α-CuSCN coordination polymorph.29 Although present in both 10 and 20% added CuTC 3-D-printed samples, these distinct ν(C–N) vibrations were markedly absent from spectra collected from the cast epoxy resin with ν(C–S) band at ~742 cm−1 shifted to a slightly higher wavenumber.
Characterisation of fabricated samples by ATR-FTIR spectroscopy. (a) Overlayed and absorbance-offset ATR-FTIR spectra of cast epoxy and 3-D-printed urethane test samples with a reference spectrum collected from neat CuTC. Shaded areas in the IR spectra are shown as zoomed panels noting: (b) distinctive ν(C–H) and ν(N–H) stretching vibration (2830–3000 cm−1) in both types of fabricated samples; (c) doublet peaks observed at 2110 and 2152 cm−1 for ν(C–N) vibration typical of the α-CuSCN polymorph; and (d) the shift or absence of details characteristic of metal-thiocyanate bonds at ~742 and 860–880 cm−1 in the cast epoxy resins with added CuTC.
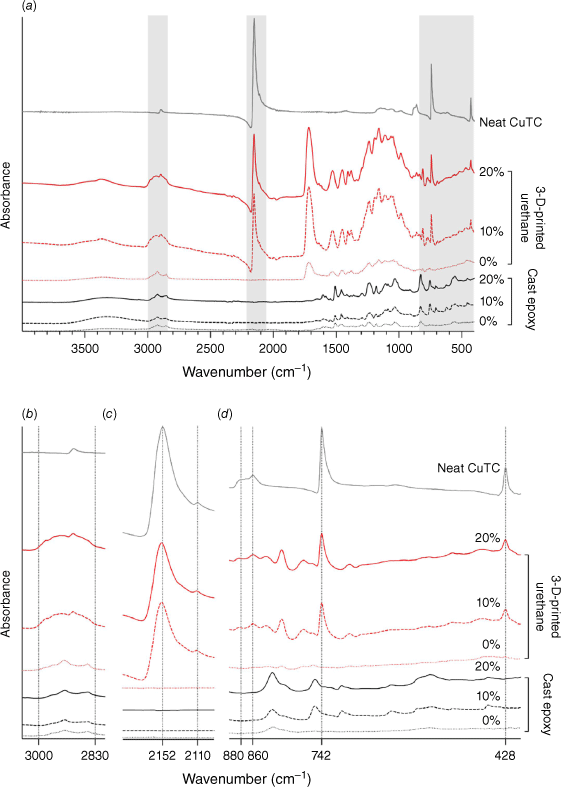
Four-angle polarised S-FTIR mapping measurements were performed on both surface and cross sections (Fig. 4), to further characterise molecular structures of the added CuTC biocide in the test samples. The 2140–2165-cm−1 spectral range was used to visualise ν(C–N) peak intensity that reflected thiocyanate distribution within the representative 60 × 60-µm2 area and to examine for altered molecular orientation attributable to modified metal-thiocyanate bonds. Both surface and cross sections of 3-D-printed test materials showed inconsistent distributions of high-intensity of thiocyanate, suggestive of incomplete dispersion within the resin matrix used for additive manufacturing. Although ~20-fold less intense, the spatial distribution of the ν(C–N) peak in cast epoxy resin surfaces and cross sections was markedly more ordered and homogenous.
Non-polarised and four-angle polarised S-FTIR maps of ν(C–N) (2140–2165 cm−1) on surface and liquid nitrogen-exposed cross sections of fabricated materials containing 20% (w/w) CuTC. Representative images depict thiocyanate distribution in (a) cast epoxy resin; and (b) 3-D-printed urethane. Note differences in intensity scales used.
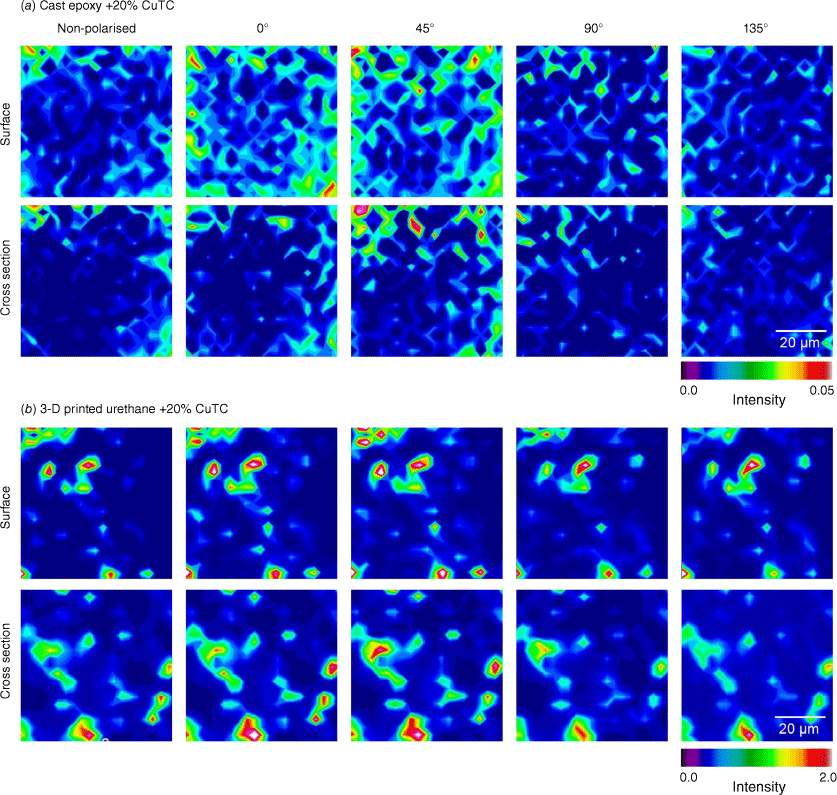
Imaging of surface microstructures by SEM revealed morphological differences between the two fabricated materials containing the same CuTC biocide (Fig. 5). Cast epoxy resins had macro-porous surfaces with microscopic pores observed in cross sections, whereas 3-D-printed materials appeared free of any obvious structural voids or fissures.
Field performance of test samples
Fouling-resistant properties of the fabricated and characterised test samples were evaluated by subsurface-immersion in a marine environment for 3 months, during which they were visually inspected at different time points (Fig. 6). Both cast epoxy and 3-D-printed urethane controls (0% added CuTC) showed marked fouling with aquatic macro-organisms by the end of the study period; with a combination of barnacles, calcareous tubeworms and bryozoans colonising the surface of the cast epoxy resin sample within 7 days of deployment and completely encrusting it within 3 weeks. The 3-D-printed test samples did not foul as rapidly overall; after the initial formation of biofilm there was no appreciable macro-fouling until the appearance of scant calcareous tubeworms and bryozoa from 5 weeks and more marked calcerous and macroalgal fouling by the trial’s end.
Progressive fouling of test samples over a 3-month trial. Samples of (a) cast epoxy and (b) 3-D-printed urethane resins were submerged under the test raft and photographed 5–6 times over the study duration. Single arrows between photos represent 1-week intervals.
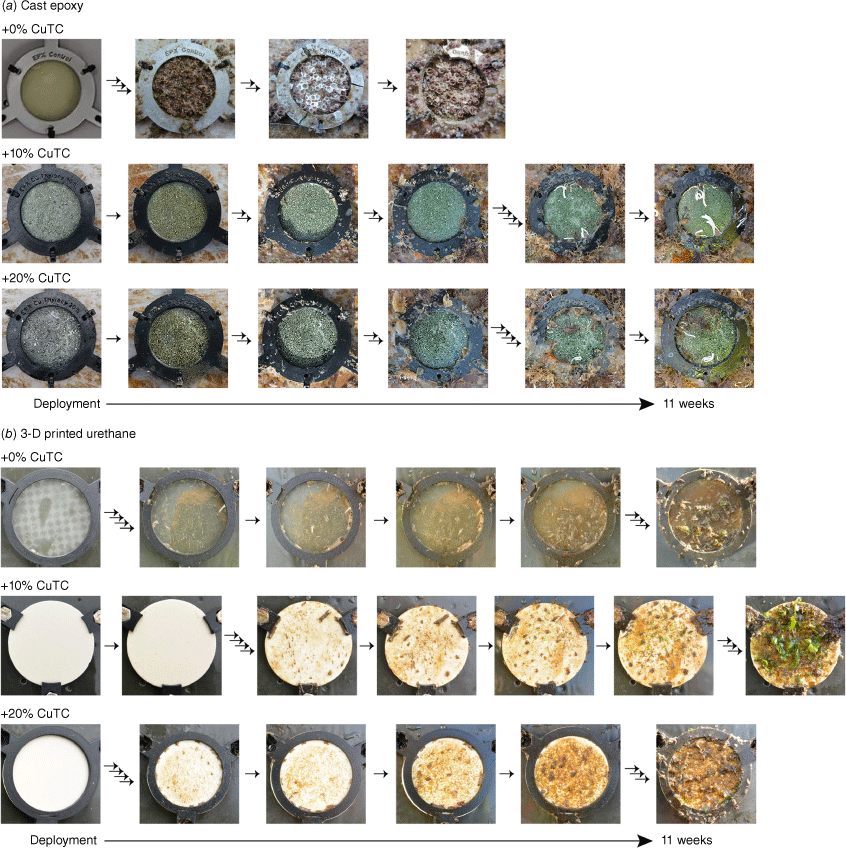
When compared to the biocide-free controls, cast epoxy resins with added CuTC were clearly more resistant to colonisation by local filter-feeding invertebrates. The surface of the 10% added CuTC test sample appeared covered by a biofilm within 1 week, with small transient bryozoan colonies appearing from week 3, followed by tubeworms, macroalgae and more persistent bryozoan colonisation from week 9 until the trial concluded. Even so, surface coverage at 11 weeks was substantially less marked than the complete obstruction that was observed in the control cast epoxy sample. The more concentrated 20% added CuTC epoxy resin showed similar fouling characteristics, with the appearance of bryozoan and tubeworm accumulations delayed until week 9. There was no clear difference in macroscopic fouling between the two compositions tested at the end of the trial. Both samples showed accrual of fouling along the surface interface with the supporting PLA clip, which also showed evidence of invertebrate colonisation within 1 week. No macroalgal growth was observed on any cast resin examined, including the biocide-free control.
Printed resins containing dispersed CuTC performed broadly similar to the biocide-free controls. Biofilms were apparent after 1 week, preceding the appearance of bryozoans from week 5 and then macroalgal growth that started at approximately week 7 and was robust by the study conclusion. Differences between the added CuTC compositions were limited to the distribution of bryozoan encrustations and the types of algal growth, whereas the time point when phyla were first observed was consistent and appeared unaffected by the amount of added biocide.
Discussion
Both cast epoxy discs and 3-D-printed urethane resins that contained CuTC were more resistant to macroscopic surface fouling when compared to the biocide-free controls. However, any improvement in the performance of 3-D-printed urethane samples over untreated base material was marginal by the trial’s end, at which point all test samples fabricated using the SLA had been extensively colonised by a number of aquatic species. The effects of adding CuTC to a pre-cured epoxy resin were more obvious; discs without added biocide near-completely fouled within 3 weeks whereas both samples containing both 10 and 20% CuTC showed surfaces clear of fouling at the end of the study.
The assumed mechanism of fouling resistance in the fabricated materials was based on the contact antimicrobial properties of copper-based biocides.30 Dispersal of the 10–20% (w/w) CuTC in the pre-set resin was expected to create surfaces resistant to marine growth. However, as shown by the S-FTIR maps of ν(C–N) in Fig. 4, there were distinct differences in dispersal at the micro scale when comparing the two material types.
The fouling-resistant properties of cast epoxy resins containing CuTC, particularly given the apparent oxidation of copper while curing (as indicated by the green colouration of the cured material), were somewhat unexpected. At the macro scale CuTC appeared to disperse well in the 3-D-printed urethane resin and the absence of any distinct evidence of chemical modification to the CuTC suggested the SLA-fabricated test samples were an efficient dispersion of a known and widely used antifouling agent.
By contrast, the colour change observed in the two-part cast epoxy resins clearly indicated a chemical reaction involving the added metalorganic had taken place during fabrication. The bioactive properties of CuTC are generally attributable to copper biochemistry30 and applications using it as an antifouling additive to paint assume the mechanism of action depends on a low rate of copper release into seawater.14 This distinctive evidence of oxidative modification to the added copper(I) indicated the deployed cast epoxy resins no longer contained a dispersed mixture of solely the original ɑ- and β-CuSCN.
The commercial KINETIX H120 cross-linking hardener used to produce the epoxy samples is a mixture of two primary amines; triethylenetetramine and isophoronediamine, and 2,4,6-tris(dimethylaminomethyl) phenol; all at percentage (w/w) concentrations. Knowing that CuTC has been shown to react with substituted pyridine and aliphatic amine ligands to form adducts at room temperature and over several days,31 it can be hypothesised that the CuTC powder dispersed through the R118 epoxy resin was susceptible to nucleophilic attack by either of the primary amine hardeners used during the 48-h cure. For this trial, it resulted in two fabricated materials containing chemically distinct bioactive compounds: unadulterated CuTC, from which the S-FTIR results showed was inefficiently dispersed in a 3-D-printed urethane matrix and a new organometallic framework resulting from reactions with added amine ligands.
Observations that support this hypothesis include the appearance of similar low 2θ peaks (as noted by arrows in Fig. 2) that are indicative of copper-amine bonds in a metalorganic framework,32 as well as evidence of branched amine metal thiocyanates in the infrared spectra.33 New bands at high wavenumbers that are normally attributed to ν(N–H) in copper amine complexes were also observed,34 as was absorption bands in regions similar to those of other reported series of copper(I) thiocyanate-amine coordination networks.31
Despite the extensive molecular evidence that CuTC was not chemically modified by the SLA additive manufacturing process, the inability of this well-established and widely used biocide to impart substantial fouling resistance is still likely an effect of the fabrication method used. Although CuTC powder dispersed into both the R118 epoxy and Rapid TUFF resins well, polarised IR maps showed that the SCN distribution in 3-D-printed samples was much less uniform at the microscale. The apparent agglomeration of the dispersed powder, likely occurring during the hour-long delay while the sample was additively assembled, left microscopic areas devoid of any active biocide molecules.
Even though cast epoxy resins showed extensive evidence of molecular modification to the added CuTC, results from the fouling study clearly showed it had retained desirable antifouling properties. It can be hypothesised that the more uniform distribution creates a better interface with seawater, whereas on 3-D-printed samples the initial biofilms that support subsequent macrofouling were able to gain traction on surface spaces free of CuTC. To further investigate this idea, subsequent experiments will examine the microscopic fouling characteristics of the developed materials and examine further the interrelationships between surface morphology, biocide activity and fabrication method used. Service life is critical for any future fouling-resistant material, and the results shown here over 3 months can provide only limited information on future utility. Upscaled experiments testing these materials should examine their performance up to and over 12 months, in different environmental conditions and examine the surfaces after deployment. Laboratory testing to accurately measure environmental Cu release should also form part of future experiments.
Conclusion
Adding chemical biocides to polymers is an effective way to affect fouling-resistant properties to fabricated structures, but consideration should be given to effects that may arise from the fabrication process. For the two types of materials tested here, both of which contained the same CuTC source, there was evidence of distinctive molecular and structural differences that can be related to their performance in a 3-month environmental fouling study. Subsequent experiments should investigate scaled-up fabrication techniques to assess larger and more complex structures and how amine adduction reactions influence the biocidal activity of copper(I) thiocyanate.
Data availability
All data presented in this paper, including collected spectra, original photographs and processed graphs, is available on request from the corresponding author.
Declaration of funding
This research was supported by a Defence Science Project seed grant from the Victorian Government Defence Science Institute (DSP11329) to R. F. Piola and N. Hameed.
Author contributions
N. Hameed oversaw the project and designed the study with R. F. Piola. K. Prasad, R. F. Piola, P. J. Molino, J. Vongsvivut, and N. V. Salim performed the experiments. K. Prasad, HK, D. J. Hare, and N. V. Salim analysed the data. R. F. Piola, P. J. Molino, and N. Hameed provided supporting resources. K. Prasad and D. J. Hare wrote the paper.
References
1 Garibay-Valdez E, Martínez-Córdova LR, Vargas-Albores F, Emerenciano MGC, Miranda-Baeza A, Cortés-Jacinto E, Ortiz-Estrada ÁM, Cicala F, Martínez-Porchas M. The biofouling process: the science behind a valuable phenomenon for aquaculture. Rev Aquac 2023; 15: 976-990.
| Crossref | Google Scholar |
2 Dürr S, Thomason JC. Biofouling. Blackwell Publishing Ltd; 2010. 10.1002/9781444315462
3 Amara I, Miled W, Slama RB, Ladhari N. Antifouling processes and toxicity effects of antifouling paints on marine environment. A review. Environ Toxicol Pharmacol 2018; 57: 115-130.
| Crossref | Google Scholar | PubMed |
4 Qian P-Y, Cheng A, Wang R, Zhang R. Marine biofilms: diversity, interactions and biofouling. Nat Rev Microbiol 2022; 20: 671-684.
| Crossref | Google Scholar | PubMed |
5 Weber F, Esmaeili N. Marine biofouling and the role of biocidal coatings in balancing environmental impacts. Biofouling 2023; 39: 661-681.
| Crossref | Google Scholar | PubMed |
6 Pistone A, Scolaro C, Visco A. Mechanical properties of protective coatings against marine fouling: a review. Polymers 2021; 13: 173.
| Crossref | Google Scholar | PubMed |
7 Chen L, Duan Y, Cui M, Huang R, Su R, Qi W, He Z. Biomimetic surface coatings for marine antifouling: natural antifoulants, synthetic polymers and surface microtopography. Sci Total Environ 2021; 766: 144469.
| Crossref | Google Scholar | PubMed |
8 Jin H, Tian L, Bing W, Zhao J, Ren L. Toward the application of graphene for combating marine biofouling. Adv Sustain Syst 2021; 5: 2000076.
| Crossref | Google Scholar |
9 Wei T, Tang Z, Yu Q, Chen H. Smart antibacterial surfaces with switchable bacteria-killing and bacteria-releasing capabilities. ACS Appl Mater Interfaces 2017; 9: 37511-37523.
| Crossref | Google Scholar | PubMed |
10 Paz-Villarraga CA, Castro ÍB, Fillmann G. Biocides in antifouling paint formulations currently registered for use. Environ Sci Pollut Res Int 2022; 29: 30090-30101.
| Crossref | Google Scholar | PubMed |
11 Thomas KV, Brooks S. The environmental fate and effects of antifouling paint biocides. Biofouling 2010; 26: 73-88.
| Crossref | Google Scholar | PubMed |
12 Salah I, Parkin IP, Allan E. Copper as an antimicrobial agent: recent advances. RSC Adv 2021; 11: 18179-18186.
| Crossref | Google Scholar | PubMed |
13 Faÿ F, Horel G, Linossier I, Vallée-Réhel K. Effect of biocidal coatings on microfouling: in vitro and in situ results. Prog Org Coat 2018; 114: 162-172.
| Crossref | Google Scholar |
14 Sandberg J, Wallinder IO, Leygraf C, Virta M. Release and chemical speciation of copper from anti-fouling paints with different active copper compounds in artificial seawater. Mater Corros 2007; 58: 165-172.
| Crossref | Google Scholar |
15 Mohammed JS. Applications of 3D printing technologies in oceanography. Methods Oceanog 2016; 17: 97-117.
| Crossref | Google Scholar |
16 Peterson E. Recent innovations in additive manufacturing for marine vessels. Marit Technol Res 2022; 4: 257491.
| Crossref | Google Scholar |
17 Garrido J, Sáez J, Armesto JI, Espada AM, Silva D, Goikoetxea J, Arrillaga A, Lekube B. 3D Printing as an enabling technology to implement maritime plastic circular economy. Procedia Manuf 2020; 51: 635-641.
| Crossref | Google Scholar |
18 Ziółkowski M, Dyl T. Possible applications of additive manufacturing technologies in shipbuilding: a review. Machines 2020; 8: 84.
| Crossref | Google Scholar |
19 Ryley M, Carve M, Piola R, Scardino AJ, Shimeta J. Comparison of biofouling on 3D-printing materials in the marine environment. Int Biodeterior Biodegradation 2021; 164: 105293.
| Crossref | Google Scholar |
20 Vongsvivut J, Pérez-Guaita D, Wood BR, Heraud P, Khambatta K, Hartnell D, Hackett MJ, Tobin MJ. Synchrotron macro ATR-FTIR microspectroscopy for high-resolution chemical mapping of single cells. Analyst 2019; 144: 3226-3238.
| Crossref | Google Scholar | PubMed |
21 Al-Qatatsheh A, Vongsvivut J, Juodkazis S, Salim NV, Hameed N. Rapidly cured multifunctional epoxy resins with switchable curing temperature and exceptional electrical properties. Adv Mater Technol 2023; 8: 2202028.
| Crossref | Google Scholar |
22 Jahromi FT, Nikzad M, Prasad K, Norén J, Isaksson M, Arian A, Sbarski I. Additive manufacturing of polypropylene micro and nano composites through fused filament fabrication for automotive repair applications. Polym Adv Tech 2023; 34: 1059-1074.
| Crossref | Google Scholar |
23 Bureau of Meteorology. Thursday, 1 June 2023 – monthly climate summary for Greater Melbourne – product code IDCKGC16L0. Canberra, ACT, Australia: Bureau of Meteorology, Australian Government; 2023. Available at http://www.bom.gov.au/climate/current/month/vic/archive/202305.melbourne.shtml
24 Bureau of Meteorology. Saturday, 1 July 2023 – monthly climate summary for Greater Melbourne – product code IDCKGC16L0. Canberra, ACT, Australia: Bureau of Meteorology, Australian Government; 2023. Available at http://www.bom.gov.au/climate/current/month/vic/archive/202306.melbourne.shtml
25 Bureau of Meteorology. Tuesday, 1 August 2023 – monthly climate summary for Greater Melbourne – product code IDCKGC16L0. Canberra, ACT, Australia: Bureau of Meteorology, Australian Government; 2023. Available at http://www.bom.gov.au/climate/current/month/vic/archive/202307.melbourne.shtml
26 Er U, Icli KC, Ozenbas M. Spin-coated copper(I) thiocyanate as a hole transport layer for perovskite solar cells. J Solid State Electrochem 2020; 24: 293-304.
| Crossref | Google Scholar |
27 Yang M, Zhu J-J, Li J-J. Synthesis and characterizations of porous spherical CuSCN nanoparticles. Mater Lett 2005; 59: 842-845.
| Crossref | Google Scholar |
28 Toeniskoetter RH, Solomon S. Infrared spectra of copper thiocyanate complexes. Inorg Chem 1968; 7: 617-620.
| Crossref | Google Scholar |
29 Kabešová M, Dunaj-jurčo M, Serator M, Gažo J, Garaj J. The crystal structure of copper(I) thiocyanate and its relation to the crystal structure of copper(II) diammine dithiocyanate complex. Inorganica Chim Acta 1976; 17: 161-165.
| Crossref | Google Scholar |
30 Vincent M, Duval RE, Hartemann P, Engels-Deutsch M. Contact killing and antimicrobial properties of copper. J Appl Microbiol 2018; 124: 1032-1046.
| Crossref | Google Scholar | PubMed |
31 Miller KM, McCullough SM, Lepekhina EA, Thibau IJ, Pike RD, Li X, Killarney JP, Patterson HH. Copper(I) thiocyanate-amine networks: synthesis, structure, and luminescence behavior. Inorg Chem 2011; 50: 7239-7249.
| Crossref | Google Scholar | PubMed |
32 Iqbal N, Wang X, Yu J, Jabeen N, Ullah H, Ding B. In situ synthesis of carbon nanotube doped metal–organic frameworks for CO2 capture. RSC Adv 2015; 6: 4382-4386.
| Crossref | Google Scholar |
33 Bowmaker GA, Hanna JV. IR Spectroscopy of two polymorphs of copper(I) thiocyanate and of complexes of copper(I) thiocyanate with thiourea and ethylenethiourea. Z Naturforsch B 2009; 64: 1478-1486.
| Crossref | Google Scholar |
34 Stanila A, Marcu A, Rusu D, Rusu M, David L. Spectroscopic studies of some copper(II) complexes with amino acids. J Molec Struct 2007; 834: 364-368.
| Crossref | Google Scholar |