Mercury in natural gas: delivering accurate reservoir sampling and analysis
Janelle Lawer A * , John Babadimas A , John Bretherton A , Bernardus van Deijl A , Jack Harfoushian B , Damien Gerard C , Brian Toole D and Mark Anderson DA Woodside Energy, Perth, WA, Australia.
B SLB, Perth, WA, Australia.
C Corelabs, Perth, WA, Australia.
D Expro, Perth, WA, Australia.
The APPEA Journal 63 56-67 https://doi.org/10.1071/AJ22270
Submitted: 8 December 2022 Accepted: 2 February 2023 Published: 11 May 2023
© 2023 The Author(s) (or their employer(s)). Published by CSIRO Publishing on behalf of APPEA. This is an open access article distributed under the Creative Commons Attribution 4.0 International License (CC BY).
Abstract
Natural gas is a critical part of the world’s energy supply and plays an important role in the transition to lower-carbon energy sources. The industry’s ability to process natural gas safely and efficiently will continue to rely on an accurate understanding of feed gas composition and contaminants, particularly in enabling future developments via existing infrastructure. Mercury is toxic to organisms, highly volatile and produced from hydrocarbon basins globally. Trace mercury concentrations in the hydrocarbon stream can potentially introduce liquid metal embrittlement hazards to industrial equipment, including cryogenic heat exchangers used to refrigerate liquefied natural gas. Inaccurate measurement of mercury levels can lead to adverse impacts measurable across the areas of health, process safety, environment, operations, waste disposal and decommissioning. Worldwide, significant project cost overruns and processing incidents have resulted from the uncertainty of mercury concentrations in hydrocarbon streams. Successful mercury management ideally begins early in a project’s lifecycle with development decisions informed by accurate measurement of mercury concentrations from reservoirs. Historically, this has been problematic, as mercury contamination and scavenging often result in a large range of uncertainty. The results from a multi-company collaborative study to reduce mercury uncertainty with new downhole sampling techniques will be shared in a case study, including production insights from the Julimar Field, west coast of Australia. The recommendations, procedures and operational best practices discussed will be applicable across the industry and beneficial to any party considering the impact of mercury in the development and processing of natural gas resources.
Keywords: background, chamber, cleaning, contamination, downhole, mercury, residual, scavenging.
Introduction
Successful management of mercury in hydrocarbon processing streams is greatly enabled by the accurate and precise measurement of reservoir concentrations early in a project’s lifecycle. Accurate data supports optimal facility design and decisions. Inaccurate characterisation of mercury concentrations has the potential to adversely impact the health, process safety, environment, design, operating costs, waste disposal, product sales and the decommissioning of an asset. Globally, significant project cost overruns have occurred due to an inadequate understanding of mercury levels in hydrocarbon fluids until late in the project development lifecycle (Chalkidis et al. 2020).
Mercury is a highly volatile element that has a strong affinity for organic matter. It is soluble in natural gas and condensates and present in hydrocarbon basins globally, exhibiting a wide range of concentrations (Chalkidis et al. 2020). The physical, chemical and geochemical properties of mercury create complex distributions in hydrocarbon systems (Yan et al. 2017). Through the process of thermal evolution, mercury concentration in hydrocarbons can be influenced by source rock origin, migration pathway and fluid chemistry (Yan et al. 2017). Historically, downhole samples are a poor quantitative indicator of mercury concentration in reservoir gas with data observed to span up to several orders of magnitude from a single reservoir source.
The studies and recommendations shared in this paper include an in-depth assessment of the impact of residual mercury in sampling systems and the processes to improve the accuracy of mercury sampling, through effective identification, quantification and prevention of mercury contamination, and scavenging from reservoir to laboratory.
Originally introduced at APPEA (Lawer 2021), this study is the result of the collaborative efforts from individuals representing various companies across the industry, including independent commercial laboratories, a service provider and an operator working together to eliminate variables, develop and test novel procedures, cross-check analyses results, and demonstrate repeatable analysis of case study samples using a variety of equipment and personnel.
A development project in the Julimar Field, northwest Australia, was the driver behind studies to improve the quality of mercury sampling and analysis. Located in a geographic region with mercury concentration uncertainty spanning up to three orders of magnitude, the Julimar Field produces to a facility with requirements to blend mercury concentrations to less than 51 µg/Nm3. To support this specific production scenario, a specialised downhole sampling program was developed with the primary objective of delivering accurate and precise downhole mercury analysis to facilitate blended gas production within the commercially defined fluid compositional range. Significant improvements in achieving downhole sampling and analysis repeatability were developed to reduce reservoir mercury concentration uncertainty and support key development decisions for the Julimar Field.
Recommendations for pre-job preparation, sampling operations and analysis are shared in this paper, along with mercury concentration results from the Julimar Field’s downhole, clean up and production sampling programs. The recommendations and results shared in this paper are applicable across the industry, to any asset, development or project requiring a better understanding of mercury concentration in their reservoirs.
Mercury concentration uncertainty
Contamination and scavenging processes
An accurate analysis of mercury concentration starts with the acquisition and preservation of a representative sample of reservoir fluids. Reservoir samples are prone to mercury contamination and scavenging due to the high reactivity of mercury in a sampling system when exposed to a range of reservoir pressure and temperatures, drilling fluid interactions, exposure to downhole tool hydraulic and mechanical components, changing conditions over transit time, and unknown sample chamber history.
Industry best practice fluid samples for mercury analysis are acquired in stainless-steel chambers coated with an inert silicon coating designed to minimise mercury adsorption into exposed metallic surfaces (Harfoushian 2013). Chambers are sealed at reservoir pressure and typically experience several days to weeks of transit before undergoing laboratory analysis.
Contamination of reservoir samples occurs with residual mercury desorbing from sampling equipment under changing pressure, temperature, time and/or chemical conditions. Desorption of residual mercury into live reservoir samples results in a contaminated or higher than representative reservoir sample. Residual mercury contributing to contamination can be present in equipment with past exposure to high mercury concentration fluids and insufficient cleaning treatments.
Scavenging of mercury from live reservoir samples occurs with mercury adsorption over time to raw metallic surfaces, inert coatings with physical damage or imperfections and hydraulic fluids in the sampling system. Adsorption of mercury into the sampling and analysis equipment results in a scavenged or lower-than-representative reservoir sample. Adsorption of mercury is more likely in sampling systems with insufficient quality control, chamber preparations and operational planning.
Sampling systems with industry-standard preparations can contain a combination of variables contributing to contamination and scavenging, resulting in downhole sample data spanning several orders of magnitude. The processes are described in Fig. 1.
Mercury contamination and scavenging processes in gas and equipment (a) the adsorption of mercury to sampling equipment results in a scavenged gas; (b) the desorption of residual mercury from sampling equipment results in contaminated gas; (c) in many systems, both processes will occur unless optimal preparations for cleaning and quality control are used to minimise mercury contamination and scavenging.
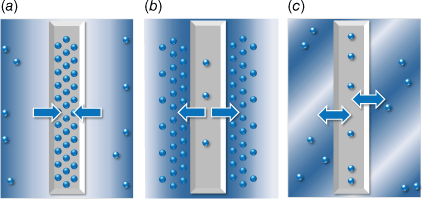
Sample analysis methodology
The primary analytical methods used for the determination of mercury in samples separate mercury from the gas or liquid ‘carrier’ fluids and allow analytical determination of concentration. Atomic fluorescence spectrometry (AFS) and cold vapour atomic absorption spectrometry (CVAAS) were the methods used in this study.
Mercury is analysed in gas using AFS or CVAAS in accordance with ISO 6978-2:2003 (ISO 2003) and ASTM D6350-14 (ATSM 2014). The process involves flowing a known volume of gas through a nickel trap filled with gold-coated sand. Due to a strong tendency to amalgamate with noble metals, mercury is adsorbed on the trap. Analytical determination of concentration in gas is measured using the fluorescence (AFS) or absorbance (CVAAS) of mercury vapour at 253.7 nm.
Mercury is analysed in liquids using CVAAS in accordance with ASTM D7623-20 (ATSM 2020). The process involves vapourising the liquid and adsorbing mercury on a gold amalgamator trap. Analytical determination of concentration in liquid is measured using the absorbance (CVAAS) of mercury vapour at 253.7 nm.
All the laboratory tests in this paper were conducted using these techniques on commercial laboratory equipment. Each gas or liquid was analysed with a minimum of two replicate samples with a focus on demonstrating repeatability between laboratories and analysis equipment. Throughout this study, two independent commercial laboratories worked side by side to deliver quality control checks and develop procedures to deliver repeatable analyses.
Developing mercury in methane ‘gas standards’
To facilitate experiments, a series of methane ‘gas standards’ were developed with a range of mercury concentrations. A mercury-free or pure methane (0 µg/Nm3) ‘gas standard’ was used to background test sample equipment and as the base for other gas standards. The clean methane was doped to create a set of gas standards at 3, 60, 125 and 300 µg/Nm3.
Achieving mercury concentration stability in the range of gas standards required significant time, effort, and the application of extensive laboratory experience and specialist techniques, beginning with the development of a high mercury concentration ‘source gas’ using phase equilibration and the vapour pressure of liquid mercury. To create the source gas, a methane-filled, 4000 cc, 10 000 psi titanium piston cylinder was orientated vertically with a machined Teflon cup mounted on the piston to prevent introduced mercury from interfering with the piston seals. Pressure was maintained at 22 psi as liquid mercury was added to the cylinder, and temperature was adjusted to deliver the target mercury saturation equilibrium concentration. Conditions were maintained for a minimum of 24 h to ensure ‘source gas’ equilibrium.
To create the range of gas standards, the high-mercury source gas was transferred to clean, uncontaminated and coated cylinders for volumetric dilution with pure methane to achieve target concentrations at required pressures. Two 830 cc positive displacement sample cylinders were combined to allow delivery of clean methane to the mercury standard cylinder at higher pressures.
Mercury concentration in methane is a function of temperature and is sensitive to pressure change. While there is little research available to show relationships with mercury vapour concentration in gases relative to pressure change, it was noted in this experimental setup a small increase in pressure resulted in a reduced mercury concentration which resulted in volumetric limitations on the creation of gas standards above 300 µg/Nm3.
Agitation of the gas standard cylinders was essential to achieve homogeneity of the mercury in vapour phase prior to use in an experiment. The concentration of each gas standard was verified before use.
Mercury contamination of sampling systems
Background checking sample chambers
Mercury-free methane was used as a carrier gas to investigate the presence of residual mercury in sample chambers cleaned to industry standards using a high-pressure water wash and dilute nitric acid. Chambers filled with pure methane were found to release significant concentrations of residual mercury (Fig. 2). In line with observations from other studies (Enrico et al. 2020), at temperatures above 80°C, mercury was observed desorbing from chamber walls and inert linings into the gas phase.
Mercury concentration in methane-filled sample chambers after industry- standard cleaning (range 18–194 µg/Nm3). None of these sample chambers qualified for use in this study (using a clean threshold of <5 µg/Nm3).
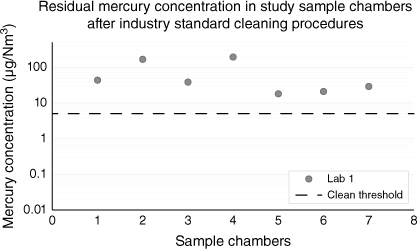
Most of the chambers in Fig. 2 were close to or exceeded the mercury concentration range of interest (<51 µg/Nm3) for the upcoming Julimar case study. If used offshore in the sampling program, filling these chambers with reservoir gas would immediately result in unrepresentative samples. For this reason, a background mercury concentration of less than 5 µg/Nm3 (approximately 10% of the maximum concentration of interest for Julimar Field) was selected as a clean threshold appropriate for supporting repeatability in experimental analysis and field operations for the case study.
Pure nitrogen was also tested as a carrier fluid for background checking of contamination. Results in Table 1 show nitrogen recovering significantly less residual mercury than methane as the first pass in the same chamber. Methane was observed in this and other experiments to act as a residual mercury ‘scrubber’ in chambers, consistent with mercury having a high affinity to hydrocarbons. All future background checks were conducted using methane as the carrier gas.
Residual mercury (µg/Nm3) | Prior number of sample jobs | Nitrogen (20°C) | Methane (20°C) | Methane (100°C) |
Chamber #1 | 2 | 3.4 | 22.78 | 38.29 |
Chamber #2 | 9 | 4.6 | 10.50 | 43.42 |
Chamber #3 | 1 | 2.0 | 53.78 | 166.6 |
A flow chart of background checking chambers for residual mercury is shown in Fig. 3.
Background checking laboratory equipment
Laboratory sampling valves, crossovers and nipples used to transfer gas to Tedlar bags were examined to improve the repeatability of the analyses. Several issues, including surface damage and the history of inert coatings, were identified as contributing potential mercury contamination to the system.
Fresh inert-coated valve assemblies were acquired and cleaned by baking at 140°C for 16+ h and purging with nitrogen at 140°C. To qualify for future use in these studies, the mercury concentration across a valve assembly was required to be less than 2 µg/Nm3.
Background air concentrations in the two laboratories used in the studies were tested and recorded between 0.2 µg/Nm3 (not considered significant) and non-detectable levels.
Mercury scavenging in sampling systems
Sample chamber coatings
To reduce the scavenging and adsorption of mercury, gas samples must be prevented from direct contact with the metal surfaces of the sample chamber cylinder, valves and piston. Chemical vapour-deposited (CVD) silicon coatings are designed to improve mercury inertness of steel, stainless steel and alloys to all metal surfaces potentially being exposed to the gas sample (Harfoushian 2013).
Prior use can introduce scratches from the activation of chamber pistons or mud solids, resulting in exposure to raw metal, exposure from imperfections in the coating and scavenging by residual solvent wash chemicals. All of these factors can potentially scavenge significant amounts of mercury from a reservoir sample.
To successfully reduce mercury scavenging, the use of a high-quality, fresh, inert coating is highly recommended for all chambers used in mercury sampling operations.
Operational techniques
Wellbore trajectory
If sampling for mercury analysis is the primary sampling objective, the borehole trajectory, formation stability and impacts on downhole sample retrieval should be made during the early stages of well design to improve the chance of sampling success. Downhole tool conveyancing methods may be considered to reduce the risk of lost chambers or fishing operations in deviated or higher-risk boreholes.
Drilling fluids
Filtrate invasion into the formation has the potential to contribute to the scavenging of mercury during downhole sampling. Consideration should be taken when choosing the optimal drilling fluid to minimise mercury losses. Reducing filtrate invasion into the formation will result in less contact with foreign fluids and maximise the chance of acquiring a representative sample. It is recommended to minimise overbalance when drilling and prioritising the sampling run as soon as the reservoir section is penetrated. Water-based drilling fluids are recommended to reduce exposure to base oils and components of synthetic-based muds likely to absorb or introduce mercury into a system.
Regardless of the type of drilling fluid used, mud samples should be acquired and analysed for mercury contamination and to support sample chamber analysis after a sampling campaign.
Sample probes
Field experience has shown that the optimal sampling technique to minimise filtrate contamination is to use focused sampling probes (Del Campo et al. 2006; Harfoushian 2013). Focused sampling probes can divert a stream of filtrate away from the centre of the probe and result in a cleaner, more representative sample. Optical fluid analysers allow the sampled fluid to be observed cleaning up in real time.
Focused probes and optical analysers are recommended for use in mercury concentration sampling programs.
Downhole pumps
Moving parts of a hydraulically operated downhole pump can potentially scavenge mercury. It is recommended to minimise the flow path between the sampling probe and the sample receptacles by removing the pumps from the sample flow path. Ideally, the wireline formation tester string is configured with sample receptacles placed immediately next to the sampling probe. If tools cannot be arranged to accommodate the recommended configuration, thorough testing for contamination and scavenging with known mercury concentration ‘gas standards’ is recommended prior to qualification for operations.
Dead volumes
The multi-sampler module of a wireline formation testing tool string incorporates a set of valves to allow formation fluid to be directed to a desired sample receptacle during sampling operations. Commonly referred to as ‘dead volume’, a small void exists between the valves of the multi-sampler module and a sample chamber. This volume is often filled with deionised water to prevent a pressure shock when a valve is opened. Although the introduction of a relatively small volume of deionised water into a chamber does not compromise the integrity of a sample, it is recommended to keep the dead volumes blank (filled with air) to prevent the introduction of foreign fluids into a sample chamber. It is recommended to first confirm that an induced pressure shock will not compromise the sampling process, given the specific operational conditions of a program.
If dead volume fluids must be used, it is recommended fluid samples are thoroughly background tested and accounted for in sample analysis procedures.
Repeatable mercury concentration sampling and analysis procedures
Thermal desorption cleaning procedures
Using the learnings from investigations into contamination and scavenging, a cleaning process involving temperature, pressure and time elements was developed to desorb residual mercury from freshly inert-coated sample chambers and prevent contamination of sampled reservoir fluids.
The steps for thermal desorption chamber cleaning are:
Apply a fresh inert CVD coating to sample chambers
Visually inspect the chamber cylinder and components for damage to the CVD coating
Bake in a ventilated downhole tool oven for 24 h at 175°C (to allow mercury desorption)
Cool, re-assemble and evacuate air from the chamber with a vacuum pump
Fill with mercury-free methane at ~1500 psi
Heat to 140°C and ~2000 psi pressure with the chamber piston fully extended (for maximum internal surface area exposure)
‘Methane soak’ overnight
Analyse gas sub-samples for mercury
Qualify ‘clean’ sample chambers for use based on a predetermined threshold.
The presence of methane with increasing temperature, pressure and time is observed to act as a ‘scrubbing agent’, efficiently desorbing mercury from freshly coated chambers and reducing the impact of residual contamination. In this study, any chamber that exceeded a background mercury concentration of 5 µg/Nm3 was re-cleaned or removed from the program if elevated concentrations continued.
After thermal desorption cleaning, 44 sample chambers in the study were analysed and demonstrated as clean with background concentrations of less than 5 µg/Nm3 (Fig. 4).
Mercury concentration in methane-filled sample chambers after thermal desorption cleaning. All sample chambers qualified for use in this study at <5 µg/Nm3.
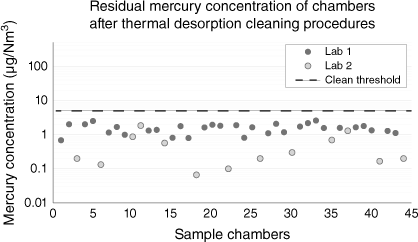
The thermal desorption procedure is a highly recommended sample chamber preparation step prior to sampling operations.
Mercury mass balance analysis procedure
If not correctly accounted for, analysis results can be compromised by processes such as mercury partitioning among fluid phases, species interconversion and the adsorption of mercury to physical chamber surfaces. Mercury mass balance experiments in this study used the volumetric and analytical data of all fluid phases and chamber washes to provide insights into mercury behaviour in downhole sample chambers and to develop a methodology to reliably quantify concentrations in reservoir gas. Mass balance analysis has also been used to verify the total concentration of mercury in a gas sample regardless of the relative concentrations of mercury left in the gas phase, partitioned or absorbed into the liquid phases (condensate, water, drilling fluids, and chamber washes), or adsorbed onto chamber surfaces.
The recommended mercury mass balance procedures are:
Confirming the ‘gas standard’ concentration as the reference point for mass balance
Transferring ‘gas standard’ to a thermal desorption cleaned sample chamber and stabilised approximately 1 h
Increasing pressure and temperature cycles over time
Extraction of sub-samples and analysis of mercury concentrations
Washing of chambers with background checked fluids:
Mercury content of all hydrocarbon phases and post-wash liquids incorporated in mass balance analysis.
In this study, the lixiviant wash had a background mercury concentration of 1.81 ng/mL and the HAC a background of 0.28 ng/mL. These background concentrations were corrected for in mass balance procedures.
It was observed that most of the mercury left in the chamber was captured by the first lixiviant wash (approximately 98%), whereas water washes contained minimal amounts of mercury. A double lixiviant wash was tested for enhanced mercury recovery, but the second wash gave a similar concentration to the HAC wash (approximately 2%), and only one lixiviant wash was used for future analysis.
Full mercury mass balance, including all hydrocarbon phases and wash fluids, is a highly recommended procedure for representative mercury analysis. The procedure is illustrated in the flow chart in Fig. 5.
Behaviour of mercury in sample chambers
Experiments designed to understand the behaviour of mercury in sample systems were performed on multiple chambers using the gas standards developed for this study. Each mercury standard was analysed to confirm the concentration prior to use, and chamber cleaning procedures were used to ensure that unwanted mercury contamination did not impact experimental results.
Impact of transit time
Long-term tests were conducted to simulate sample chambers undergoing sampling operations at reservoir temperature and pressure before transportation over approximately 2 weeks. The purpose of this test was to examine the recovery of samples and the behaviour of mercury in clean, uncontaminated chambers over multiple days after restoration to elevated temperature and pressure. Throughout these simulations, the mercury concentration was tested and recorded over time for a low mercury standard (30 µg/Nm3) and a high mercury standard (300 µg/Nm3) (Fig. 6).
Long-term mercury concentration ‘transit’ tests on (a) low 30 µg/Nm3 gas standard with 96% average recovery when restored to high pressure and temperature; and (b) 300 µg/Nm3 with 97% recovery when restored to high pressure and temperature, dropping to 89% recovery over 2 days at the same conditions.
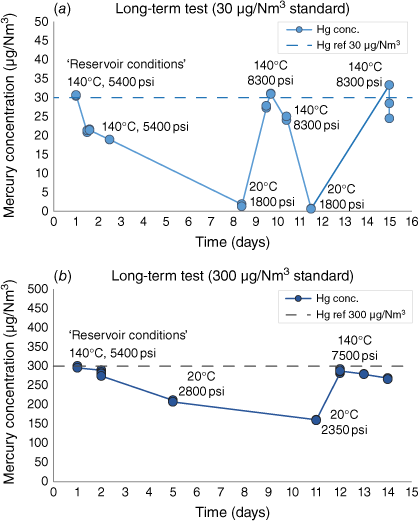
The low gas standard 30 µg/Nm3 experiment (Fig. 6a) recovered an average of 96% of the initial mercury concentration. This test shows an intermediate step increase in pressure and temperature around day 10, also recovering close to 100% of the initial concentration, before undergoing another cooling and heating cycle.
The final high-pressure, high-temperature measurements in the high gas standard 300 µg/Nm3 experiment (Fig. 6b) reached 292 µg/Nm3 (97%) recovery of initial mercury concentration and declined over 2 days to 266 µg/Nm3 (89%) at the same pressure and temperature conditions.
Both experiments show declining mercury concentration over time, although maintaining pressure and temperature can be recovered.
These results demonstrate the value of significantly increasing temperature and pressure to achieve reasonable recovery into the gas-only phase. Depending on fluid composition (e.g. condensate gas ratio), it is recommended that gas-only concentrations be considered indicative without lixiviant washes, rinses and full mass balance procedures.
Mercury partitioning
Depending on experimental conditions, the total mercury introduced to a sample chamber can be variably distributed between the gas phase, liquid phases and adsorption to the sample chamber walls. Three tests were conducted to show mercury partitioning of a 303 µg/Nm3 gas standard as a function of an experimental state, temperature, pressure and chamber history (Fig. 7).
Mercury partitioning test and mass balance results. (a) partitioning in a chamber not previously exposed to lixiviant, sub-sampled with ‘rapid hot gas blow down’ while held at constant pressure, (b) partitioning in a chamber not previously exposed to lixiviant, subject to ‘cold gas blow down’ at 20°C in a depressurised chamber, (c) partitioning in a chamber used in prior experiments, including exposure to lixiviant washes, subject to ‘cold gas blow down’ at 20°C in a depressurised chamber.
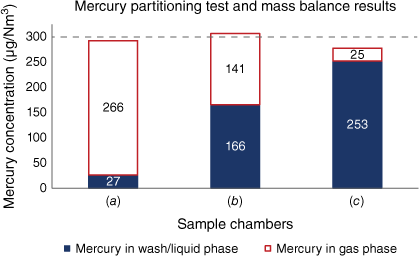
The use of a ‘rapid hot gas blow down’ sub-sampling technique (Fig. 7a) is operationally more complex and requires maintaining constant temperature and pressures throughout sub-sampling. This technique has been shown to retain the most mercury in the gas phase and could be used for early, indicative gas-only mercury concentration insights.
The use of a ‘cold gas blow down’ sub-sampling technique (Fig. 7b, c) simplifies sub-sampling operations in the laboratory by using ambient temperature and depressurised chambers. The ‘cold gas blow down’ technique is shown to maximise condensed mercury on the chamber walls, thereby allowing optimal recovery with the use of washes and full mass balance calculations. It is worth noting that the chamber in Fig. 7c was washed with lixiviant in a prior experiment, and despite recovering over 90% of the mercury in the gas standard with mass balance in this experiment, this chamber would not be recommended for use in field operations due to the likely presence of residual solvents and the increased risk for mercury contamination or scavenging, including the potential for a compromised inert lining. Once a chamber has been used in an experiment, exposed to mercury and washed with lixiviant, it is recommended to be recoated and put through the thermal desorption cleaning process before being considered for use in field operations or most studies.
Gas-only mercury concentrations in pure methane in a laboratory setting are shown in Fig. 7 to vary widely with operational techniques and sampling conditions. The recommended sub-sampling technique to obtain representative mercury concentrations from a chamber of potentially partitioned reservoir gas is ‘cold gas blow down’ combined with chamber washes and full mass balance procedures.
Case study: Julimar Field, Carnarvon Basin, Western Australia
Julimar sampling campaign
The Julimar Field, offshore northwest Australia, comprises stacked independent fluvial sandstone reservoirs in a region of historically variable mercury concentrations in gas. The primary objective of the Julimar downhole sampling program in 2020 was to support blended production of the reservoirs to a natural gas commercial specification of <51 µg/Nm3 mercury. The Julimar sampling program presented an ideal opportunity to apply the recommendations of the studies with the intent of delivering statistically representative, relatively low mercury concentration results, repeatable within a single chamber, reservoir, and across a range of equipment and laboratories.
All sample chambers in the program, including backups, were fresh coated, cleaned and baked with the thermal desorption procedure to minimise mercury contamination. Background checks of the cleaned sample chambers included filling sample chambers with pure methane and verifying that background mercury concentrations were at elevated temperature and pressures.
All sample chambers for Julimar offshore operations passed the acceptance criteria of 5.0 µg/Nm3 for this study (Fig. 8). While the results from one laboratory appear consistently lower in Fig. 8, it should be noted the averages have a difference of less than 1 µg/Nm3, the two laboratories routinely and consistently cross-checked and compared a variety of gas standards and experimental techniques throughout all phases of this project with excellent repeatability, and the intent of this work is not to make commercial recommendations.
Downhole sample chambers used the in Julimar Field Sampling Program cleaned with thermal desorption techniques and background checked to <5 µg/Nm3 to qualify for use offshore. Average concentration was 1 µg/Nm3.
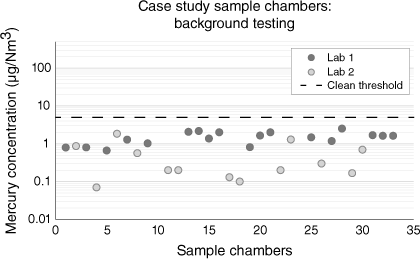
The Julimar development project targeted five fluvial channels, each an independent gas reservoir (Fig. 9). Two of the five reservoirs qualified for best practice mercury concentration sampling based on the recommendations from the study, with the primary differentiation based on drilling fluid overbalance criteria.
Schematic representation of five independent fluvial channels in the Julimar Field. Zone A and Zone C were identified as suitable for optimised sampling for mercury concentration analysis with two sample stations used per zone. Zones B, E and D did not qualify for optimised mercury concentration sampling and analysis based on overbalance criteria and tool conveyance constraints.
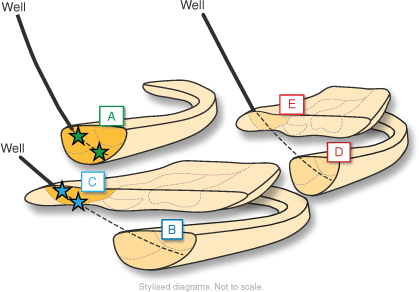
The following operational techniques were used to maximise the chance of a successful sampling campaign in the Julimar Field:
Optimal sample chamber preparations, including:
Optimal open-hole sampling conditions to minimise contamination (average contamination 0.65%):
Optimal equipment configuration to minimise contamination and scavenging:
Optimal chance of obtaining representative samples:
-
42 sample chambers filled from 2 independent reservoirs
-
Sampling from two sample stations within each reservoir (in the event of fluid segregation)
-
Acquisition of a large volume of gas (~19 L at reservoir conditions)
-
Sample analysis using washes and full mass balance procedures
-
Quality control and cross-checking results between multiple laboratories
-
Time to analysis variables tested in-field:
Julimar mercury concentration results
The Julimar sampling campaign delivered high-quality, accurate downhole mercury concentration analysis samples with excellent repeatability and less than one order of magnitude in the range measured between two laboratories. The downhole results from 2020, clean up to platform results from December 2021 to January 2022, and blended production estimates results since March 2022 are shown together in Fig. 10. Statistics for each measured data set are shown in Table 2.
Julimar mercury concentration sampling results from downhole, clean up and production estimates. Each of the clean up results is a recombination of dry gas, condensate and water measurements. The average of downhole, clean up and production data is within 10 µg/Nm3 in each zone.
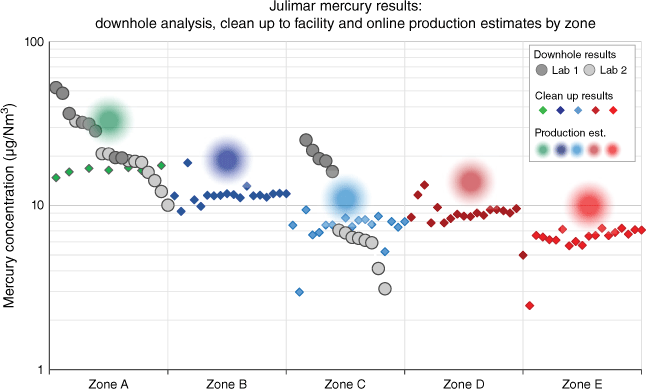
Mercury µg/Nm3 | Zone A | Zone B | Zone C | Zone D | Zone E | |||||
Downhole | Clean up | Downhole | Clean up | Downhole | Clean up | Downhole | Clean up | Downhole | Clean up | |
Mean | 25.0 | 16.4 | – | 11.8 | 11.3 | 7.4 | – | 9.0 | – | 6.4 |
Median | 20.1 | 16.4 | – | 11.5 | 6.8 | 7.6 | – | 8.9 | – | 6.6 |
St. dev. | 11.9 | 0.9 | – | 1.8 | 8.1 | 1.4 | – | 1.7 | – | 1.1 |
Range | 42.2 | 2.8 | – | 9.0 | 22.0 | 6.4 | – | 8.4 | – | 4.8 |
Minimum | 10.1 | 14.8 | – | 9.2 | 3.1 | 3.0 | – | 5.0 | – | 2.5 |
Maximum | 52.3 | 17.6 | – | 18.2 | 25.1 | 9.4 | – | 13.3 | – | 7.3 |
Count | 18.0 | 7.0 | – | 18.0 | 11.0 | 18.0 | – | 18.0 | – | 18.0 |
Downhole samples were acquired and analysed in 2020 at two laboratories. Zone A and Zone C delivered high-quality, repeatable mercury concentration results using the recommended downhole sampling and analysis techniques from the studies. Zone A data had a downhole mean of 25.0 µg/Nm3, a standard deviation of 11.9 µg/Nm3 and a range of 42.2 µg/Nm3. Zone C data had a downhole mean of 11.3 µg/Nm3, a standard deviation of 8.1 µg/Nm3 and a range of 22.0 µg/Nm3. With the objectives of the campaign achieved, the risk of blended production from the project exceeding 51 µg/Nm3 was considered low.
Well clean up (or flowback) samples for all five zones were acquired from December 2021 to January 2022 and analysed at an independent laboratory on the production facility. Each production zone was flowed for approximately 5 days from the reservoir and through 22 km of subsea pipeline to the production separator. Each of the clean up samples in Fig. 10, Table 2 is a recombination of the stable mercury concentrations of dry gas, condensate and water concentrations back to an equivalent natural gas value. The recombined data has excellent repeatability and a mean less than 10 µg/Nm3 of downhole means of Zone A and Zone C. Standard deviations range between 0.9 and 1.8 µg/Nm3, with data ranges between 2.8 and 9 µg/Nm3.
Production estimates of mercury from each zone in the blended production stream since March 2022 are shown in Fig. 10. The mercury concentration estimate in each zone is back calculated from measurements in a blended fluid stream over approximately 6 months of production and baselined relative to the means of downhole and clean up data. While production estimates appear slightly higher than clean up and downhole reservoir sample data, the results are still within 10 µg/Nm3 of the downhole reservoir means.
When comparing different data types in Julimar, downhole to clean up and production, the low absolute values must be considered along with operational variables, such as different production separators, different sampling points in the fluid streams and pipeline scavenging. Despite all these variables, the spectrum of Julimar mercury concentrations and data types confirm the accuracy and repeatability of downhole reservoir analysis when executed with the recommended techniques.
Summary
Experiments in this study show that inert-coated chambers with industry-standard cleaning and previous exposure to mercury can contaminate fresh reservoir samples
Thermal desorption cleaning procedures can remove residual mercury contamination from chambers
All laboratory instrumentation (valve manifolds, crossovers, etc.) should be checked, fresh-coated and baked before use
Creation of ‘gas standards’ of known mercury concentration requires considerable expertise
Washes and mass balance studies combining volumetric measurements and analytical data can be used to reconcile mercury concentrations in sample chambers
Transit time can be eliminated as a variable using recommended cleaning and recombination procedures
The successful application of recommended procedures to the Julimar Field sampling program delivered highly repeatable downhole reservoir results confirmed by clean up and production data
The average of downhole, clean up and production results demonstrate excellent repeatability within 10 µg/Nm3, delivering program objectives and supporting future applications of the sampling and analysis recommendations.
Conclusion
The Julimar case study required the identification, quantification and elimination of variables contributing to mercury contamination and scavenging in sampling and laboratory analysis systems. The high-quality results from the case study supported Julimar project decisions and demonstrate the progress that can be made with a multi-company collaborative team approach to problem solving.
Results and methodology are shared with the industry along with an invitation to collaborate and integrate other insights and experience to further optimise mercury concentration sampling. While the recommendations have demonstrated significant improvement in the repeatability of results and quantification of contamination and scavenging processes, it is acknowledged that mercury concentration analysis remains a specialised process. Areas of potential future study in this field could include investigating wider applications of CVD coatings, suitability for other equipment and chamber types, techniques to improve the background checking pre-operations logistic requirements along with operational requirements to support mercury sampling in increasingly complex operational environments where optimal conditions may not be achievable.
As operators potentially need to develop deeper, higher temperature and more remote hydrocarbon reserves, the challenge to manage mercury uncertainty in future production streams will increase. The ability to make fast and well-informed decisions in future developments can be supported by the application of demonstrated industry best practice mercury concentration sampling and analysis techniques.
Introduced at APPEA (Lawer 2021) and concluded at APPEA 2023, the results and recommendations from this study have been shared with the industry to support operators, service companies, laboratories and the wider industry manage the uncertainty of mercury in the development and processing of natural gas resources.
Acknowledgements
The authors wish to thank Woodside Energy and Julimar Brunello Joint Venture Partner Kuwait Foreign Petroleum Exploration Company for permission to publish this paper.
References
ATSM (2014) ‘Standard Test Method for Mercury Sampling and Analysis in Natural Gas by Atomic Fluorescence Spectroscopy’. ATSMD6350-14. (American Society for Testing and Materials) Available at https://www.astm.org/d6350-14.htmlATSM (2020) ‘Standard Test Method for Total Mercury in Crude Oil Using Combustion-Gold Amalgamation and Cold Vapor Atomic Absorption Method’. ATSMD7623-20. (American Society for Testing and Materials) Available at https://www.astm.org/d7623-20.html
Chalkidis A, Jampaiah D, Hartley PG, Sabri YM, Bhargava SK (2020) Mercury in natural gas streams: A review of materials and processes for abatement and remediation. Journal of Hazardous Materials 382, 121036
| Mercury in natural gas streams: A review of materials and processes for abatement and remediation.Crossref | GoogleScholarGoogle Scholar |
Del Campo C, Dong C, Vasques R, Hegeman P, Yamate T (2006) Advances in Fluid Sampling with Formation Testers for Offshore Exploration. (Society of Petroleum Engineers)
| Crossref |
Enrico M, Mere A, Zhou H, Carrier H, Tessier E, Bouyssiere B (2020) Experimental Tests of Natural Gas Samplers Prior to Mercury Concentration Analysis. Energy & Fuels 34, 5205–5212.
| Experimental Tests of Natural Gas Samplers Prior to Mercury Concentration Analysis.Crossref | GoogleScholarGoogle Scholar |
Harfoushian J (2013) Quantification of Low Levels of Mercury in Gas Reservoirs Using Advanced Sampling and Analysis Techniques. (Society of Petroleum Engineers)
| Crossref |
ISO (2003) ‘Natural gas — Determination of mercury — Part 2: Sampling of mercury by amalgamation on gold/platinum alloy’. ISO6978-2:2003. (International Organization for Standardization: Geneva) Available at https://www.iso.org/standard/38601.html
Lawer J (2021) Gas sampling for mercury analysis. The APPEA Journal 61, 559–562.
| Gas sampling for mercury analysis.Crossref | GoogleScholarGoogle Scholar |
Yan Q, Han Z, Wang S (2017) Geochemical Characteristics of Mercury in Oil and Gas. IOP Conference Series: Earth and Environmental Science 63, 012024
| Geochemical Characteristics of Mercury in Oil and Gas.Crossref | GoogleScholarGoogle Scholar |
![]() Janelle Lawer, Wheatstone Technical Lead, Woodside Energy. Janelle Lawer is an oil and gas professional with 20 years of experience working with supermajor and mid-size exploration and production companies in Australia and the USA. She has held roles across the spectrum of geoscience, petrophysics, reservoir engineering and technical asset and joint venture management, with a focus on delivering integrated and collaborative technical solutions. Janelle holds a Bachelor of Science (Hons I) from the University of Queensland, Australia. She is an active member of the Society of Petroleum Engineers (SPE) and will serve as a SPE Distinguished Lecturer in 2023–2024. |
![]() John Babadimas, Petrophysicist, Woodside Energy. John Babadimas joined Woodside Energy in 2016 as a Graduate Petroleum Engineer, holding assignments as a Reservoir Engineer, Production Engineer and Petrophysicist. He has been involved in operations and studies across a wide range of Woodside's assets in Australia, Western Africa and Myanmar. John holds a Bachelor of Engineering (Petroleum, Civil and Structural) from the University of Adelaide, Australia, and is a member of SPE and the Society of Petroleum Well Log Analysts (SPWLA). |
![]() John Bretherton, Senior Petrophysicist, Woodside Energy. John Bretherton is a Petrophysics Team Lead at Woodside Energy with 20 years’ experience working with exploration and production companies in Australasia, Africa, Europe and the USA. He has held team and team lead roles through planning, exploration, development and abandonment phases of a variety of international oil and gas projects. John holds a Bachelor of Geology (Hons) from the University of Derby, England. He is a member of SPWLA and SPE. |
![]() Bernardus van Deijl, Petrophysics Advisor, Woodside Energy (retired). Bernardus van Deijl has 35 years of experience in the oil and gas industry. He started his career as a Research Petrophysicist with Shell in Rijswijk, the Netherlands, followed by multiple international assignments in Shell companies. Although his primary discipline is petrophysics, Ben has worked in other disciplines, including software development and well engineering. After 20 years with Shell, he joined Woodside as a Principle Petrophysicist. During his 15 years with Woodside, he held the roles of Chief Petrophysicist and Petrophysics Advisor. |
![]() Jack Harfoushian, Reservoir Engineering Advisor, SLB (Schlumberger Australia Pty Ltd). Located in Perth, Australia, Jack Harfoushian is a Reservoir Engineering Advisor for SLB. He provides data acquisition support and interpretation for formation testing and sampling services. Jack joined SLB in 1989 and has held assignments in Europe, Africa, Middle and Far East Asia, and in Australia. Jack holds a Bachelor of Engineering degree from Curtin University, Australia, and a Master of Engineering degree in Reservoir Engineering from Heriot-Watt University in Scotland. He has authored and co-authored several publications and is the inventor of an allowed US patent. Jack is an active member of SPE and has served as a member of the SPE Distinguished Lecturers committee. |
![]() Damien Gerard, Reservoir Fluids Supervisor, Core Laboratories Australia. Damien Gerard has a BSc (Chemistry) from Murdoch University in Western Australia. He is currently the Reservoir Fluids Supervisor for Core Laboratories Australia and has been working for the company in the oil and gas industry since 1998. Damien is a Professional Member of SPE. |
![]() Brian Toole, Manager of Operations, Expro Group (retired). Brian Toole commenced his career in the oil and gas industry in 1995 as a Field Engineer working on rig automation systems before progressing into the field of reservoir fluid sampling metering and analysis. Brian has a professional background in software development and mechatronics and has spent 22 years developing skills specialising in reservoir fluid analysis and metering techniques. Brian has worked as a Field Engineer, a Product Line Manager for the Asia region and a Manager of Operations for Expro Group. Brian is a member of SPE. He holds a diploma in Computer Science and Electronics from Midland Technical College Perth, Western Australia. |
![]() Mark Anderson, Senior Chemist, Fluids Department, Expro Group Australia. Mark Anderson has over 30 years of experience in the oil and gas industry ranging from the Aberdeen oilfield service sector to field supervisory positions for Expro Group, Australia. Mark has worked on projects globally, including 5 years in Kazakhstan supervising the reservoir fluid sampling and analysis in the Kashagan Project. Recently, Mark has overseen the fluids sampling and analysis programs for Expro Group’s involvement in several major gas development projects in Australia. Mark holds a Bachelor of Science (Hons) from the University of Paisley in Scotland and is a former SPE member. |